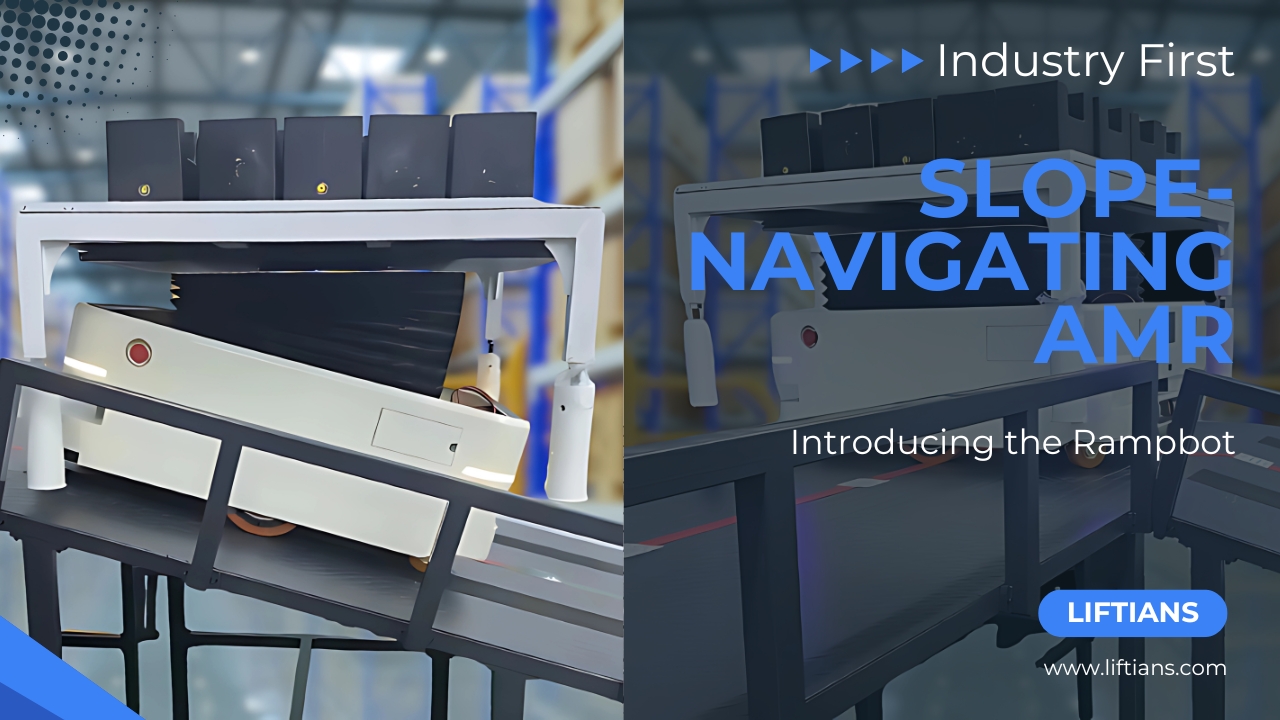
In today’s fast-paced logistics environment, keeping up with demand and maintaining operational efficiency can be a daunting challenge. While adding more labor or tweaking workflows may help temporarily, there comes a point where manual processes alone are no longer sufficient. That’s when warehouse automation becomes essential.
Automation isn’t just about adopting the latest technology—it’s about solving critical bottlenecks, reducing costs, and staying competitive in an increasingly demanding market. In this blog, we’ll explore 5 signs your warehouse needs automation and provide actionable steps to implement it effectively.
One of the most obvious signs your warehouse needs automation is an inability to handle growing order volumes. If you frequently experience delays, backlogs, or customer complaints during peak periods, your current processes may be maxed out.
Automation systems like goods-to-person technology and autonomous mobile robots (AMRs) streamline workflows by reducing travel time and speeding up picking and packing. These systems can handle higher volumes without overburdening your workforce, ensuring faster order fulfillment.
Key Insight: Automation scales with demand, so your warehouse can handle peak seasons without compromising efficiency.
If your labor costs are increasing but productivity remains stagnant, it’s a clear sign that manual processes are no longer sustainable. Hiring more workers may seem like a solution, but it often leads to diminishing returns and higher overheads.
Robotics and automated systems take over repetitive tasks like sorting, picking, and transporting goods. This reduces dependency on labor for high-volume tasks, allowing your team to focus on strategic and value-added activities.
Pro Tip: Automation doesn’t replace employees—it empowers them to work smarter and more efficiently.
Frequent picking and packing errors can lead to costly returns, wasted resources, and dissatisfied customers. If your error rates are increasing as order volumes grow, it’s time to consider automation.
Automated systems use AI-driven precision and real-time tracking to ensure accurate order fulfillment. For example, barcode scanners and vision systems verify items at every stage, reducing human error and improving customer satisfaction.
The Result: Fewer errors mean fewer returns and higher customer loyalty.
As your business grows, space constraints may start to limit your operations. Traditional storage methods often lead to inefficient use of space, making it harder to manage increasing inventory.
Automated storage solutions, like vertical lift modules (VLMs) and high-density shelving systems, maximize storage capacity by utilizing vertical space. These systems allow you to store more inventory in the same footprint, delaying or eliminating the need for costly expansions.
Why This Matters: Better space utilization means lower real estate costs and more room to grow.
Without real-time insights into inventory levels, order statuses, and workflow efficiency, decision-making becomes reactive rather than proactive. This can lead to missed opportunities and inefficiencies.
Automated warehouses leverage IoT-enabled systems and warehouse management software (WMS) to provide real-time data on every aspect of operations. These insights allow managers to monitor performance, anticipate bottlenecks, and make data-driven decisions.
Bottom Line: Real-time visibility empowers you to stay ahead of challenges and optimize your operations.
If these signs resonate with your current situation, it’s time to explore automation. Here’s how to begin:
Identify the specific challenges your warehouse is facing. Are you dealing with frequent errors, long lead times, or space constraints? Understanding your pain points will help you determine which automation solutions are most appropriate.
Clearly outline what you hope to achieve with automation. Whether it’s faster order fulfillment, reduced labor costs, or improved accuracy, having defined goals will guide your implementation strategy.
Work with a trusted partner like Liftians to select technologies that align with your goals. From robotic picking systems to real-time inventory tracking, choose solutions that address your unique challenges.
Begin with a pilot project to test the effectiveness of automation in a specific area of your warehouse. Use the results to refine your approach before scaling up.
Automation is most effective when paired with a well-trained workforce. Provide your employees with the knowledge and tools they need to operate and maintain new systems effectively.
At Liftians, we specialize in helping warehouses transition to automation seamlessly. Our tailored solutions, such as goods-to-person systems and advanced robotics, are designed to address your unique challenges and set you up for long-term success.
From identifying pain points to implementing cutting-edge technology, we’re here to guide you every step of the way.
If these signs resonate with you, it’s time to take the first step toward automation. Contact Liftians today or follow us on LinkedIn for more tips, insights, and success stories in warehouse automation. Let’s build a smarter, more efficient future for your business.